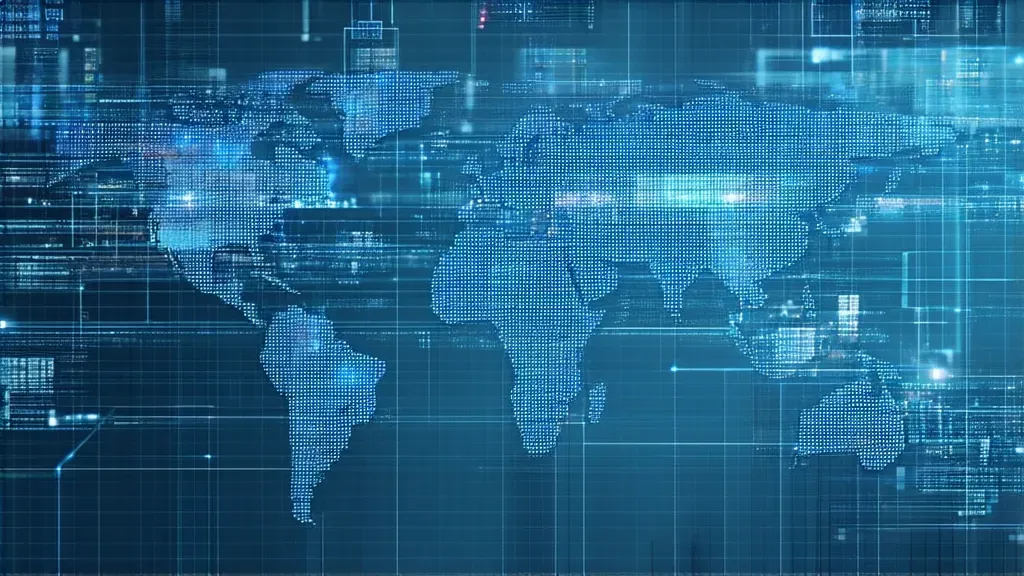
Database Management and Optimization for a Logistics Management Company
/ 4 min read
Updated:Database Management and Optimization for a Logistics Management Company (Automotive Transport)
1. Title Page
Title: Optimizing Logistics Operations through Data Management
Company: Logistics Company DACH-Region
Prepared by: Ing. Florian Zeba LL.B.
Project Date: 01.02.2022
2. Executive Summary
This case study outlines how Florian Zeba improved the data and database management system for a transportation company operating in the DACH region. The project included the expansion of the database system and the creation of an analytical dashboard to optimize transportation routes, resource allocation, and operational efficiency. The result was a significant improvement in decision-making capabilities and cost efficiency for the management.
3. Introduction
Background: The transportation company specializes in transporting vehicles for all major car brands across the DACH region. The company collected real-time data from its fleet of freight trains but lacked an efficient system to analyze and utilize this data for decision-making.
Industry Context: The logistics industry faces challenges such as route optimization, cost control, and resource management.
Objectives:
- To develop a centralized database system for real-time data collection and analysis.
- To create a dashboard that provides actionable insights for operational decisions.
- To train staff on the new system for effective adoption.
4. Problem Statement
The company faced inefficiencies due to fragmented data storage and delayed reporting processes. The lack of real-time analytics made it difficult for management to optimize routes, balance workloads, and reduce operational costs. The company required a solution that integrated data from multiple sources into a unified, easily interpretable format.
5. Analysis of the Situation
SWOT Analysis:
-
Strengths:
- Established transportation network
- Availability of rich data from sensors and reports
- Experienced management team
-
Weaknesses:
- Fragmented data storage system
- Delayed reporting processes
- Lack of analytical tools for decision-making
-
Opportunities:
- Improved efficiency through data-driven decisions
- Reduction in operational costs
- Enhanced customer satisfaction with better delivery tracking
-
Threats:
- Resistance to technological change from staff
- Data security risks
- Increased competition in the logistics sector
Industry Analysis (PESTEL):
- Political: Stable regulations but growing emphasis on sustainability
- Economic: Rising fuel costs pushing for route optimization
- Social: Increased customer demand for real-time delivery updates
- Technological: Advancements in IoT, AI, and big data analytics
- Environmental: Pressure to reduce carbon emissions through optimized routes
- Legal: Compliance with data privacy laws (GDPR)
6. Proposed Solutions and Alternatives
Solution 1 (Selected): Develop a Centralized Data Management System with Analytical Dashboards
- Pros: Real-time insights, customizable dashboards, and automated reporting
- Cons: High initial development cost and staff training requirements
Solution 2: Outsource Data Analysis to a Third-Party Service
- Pros: Lower upfront cost and quick implementation
- Cons: Less control over data and higher recurring costs
Solution 3: Upgrade Existing ERP System with New Modules
- Pros: Leverages existing infrastructure
- Cons: Limited customization and longer implementation time
Justification for Selected Solution: Solution 1 was chosen due to its potential for long-term cost savings and enhanced decision-making capabilities through tailored dashboards.
7. Implementation Plan
-
Phase 1 (Data Integration):
- Collect data from sensors, employees, and reports into a centralized SQL database (Microsoft SQL Server).
- Normalize and transform the data to create a unified data model.
-
Phase 2 (Dashboard Development):
- Develop a multi-page dashboard with KPIs and detailed filters using BI tools.
- Create a reporting function for snapshot exports.
-
Phase 3 (Training and Deployment):
- Conduct training sessions for employees and managers on using the dashboard and database tools.
- Provide user guides and ongoing technical support.
-
Phase 4 (Monitoring and Optimization):
- Gather feedback from management and refine dashboard features.
- Monitor system performance and address any issues promptly.
8. Results and Outcomes
- Operational Efficiency: Management received real-time dashboards with critical KPIs, enabling data-driven decisions.
- Resource Optimization: Improved train route planning and staff allocation based on utilization rates.
- Cost Savings: Reduced fuel costs and overtime by optimizing logistics operations.
- Process Improvement: Enhanced cross-department collaboration through centralized data access.
9. Lessons Learned
- Importance of Stakeholder Involvement: Regular feedback from management ensured the dashboard met their needs.
- Data Quality is Key: Early focus on data normalization reduced issues during analysis.
- Training Drives Adoption: Proper training minimized resistance and boosted productivity.
10. Conclusion
The project successfully delivered a real-time analytical solution that empowered management with data-driven insights, resulting in better decision-making and significant cost savings. The solution laid a strong foundation for future data initiatives within the company.
11. References and Appendices
- References: Internal project documents, SQL database architecture diagrams, and BI tool manuals.
- Appendices: Sample dashboard screenshots, SQL queries for data normalization, and training materials.
Any Questions?
Contact me on any of my communication channels: